'최첨단 제조 혁신 플랫폼'과 '인간 친화적인 제조 현장'. 현대자동차그룹이 완공한 미국 내 세 번째 생산 기지 '현대차그룹 메타플랜트 아메리카'(HMGMA)를 규정하는 한마디다.
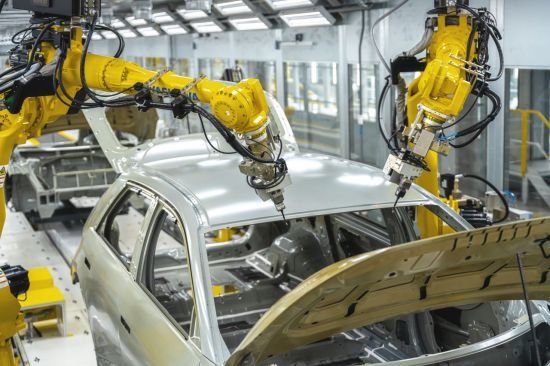
HMGMA는 싱가포르 글로벌 혁신센터(HMGICS)에서 실증 개발한 최첨단 제조 혁신 플랫폼을 바탕으로 고효율·고품질 생산을 실현했다.
HMGMA는 프레스, 차체, 도장, 의장으로 이뤄지는 자동차 생산 공정 요소마다 제조 혁신 기술이 적용됐다.
패널 홀·크랙 감지 시스템, 도어 간격. 단차 자율 보정 장착, 도어 자동 탈부착 등이 대표적이다.
수백 대 최첨단 로봇 장비들이 높은 생산성과 균일한 품질을 보장한다.
세계 최초 적용 기술인 패널 홀·크랙 감지 시스템은 프레스 공장에서 작동한다.
수십 대의 카메라를 통해 촬영한 데이터를 딥러닝으로 학습하며 AI 기반 품질 관리를 뒷받침한다.
제작된 패널들은 100% 자동화 물류 시스템을 통해 다음 공정으로 간다.
자동적재 시스템(ASRS)은 패널을 차종별로 분류해 수십장씩 팔레트에 싣고, 자율주행 운반로봇(AGV)은 이 팔레트를 다음 공정으로 적시에 옮긴다.
AGV는 동시 위치 측정 및 지도 작성(SLAM) 기술을 바탕으로 구동된다.
차체 공장은 공정 중 도어 간격·단차 자율 보정 장착 시스템을 세계 최초로 적용해 완전 자동화를 달성했다.
외관 품질 검사에서는 보스턴다이나믹스의 4족 보행 로봇 ‘스팟(Spot)’이 수행하는 사양 검사와 측정된 품질 정보를 조립 로봇으로 실시간 피드백한다.
도장 공정도 도포부터 품질 검사까지 자동화됐다.
의장 공장에는 로봇이 차량 문(도어)을 자동으로 탈거하고, 도장 후 정밀하게 장착하는 시스템을 세계 최초로 구현됐다.
14대의 로봇이 협동 제어를 통해 한 치의 오차도 없이 도어를 장착한다.
차체와 결합할 각종 자동차 부품은 200여대 자율이동로봇(AMR)이 나른다.
AMR은 SLAM 기술을 바탕으로, 물류창고에서 각 공정으로 원하는 위치까지 경로를 생성해 부품을 배달할 수 있다.
완성된 차량은 주차로봇 위에 올라타 자동화된 무인 품질 검사 등을 거친다.
과거에는 작업자가 직접 운전해 차량을 옮겨야 했으나, 인간 중심 근무 환경 조성으로 작업자의 신체 부담을 줄이고 부상을 예방한다.
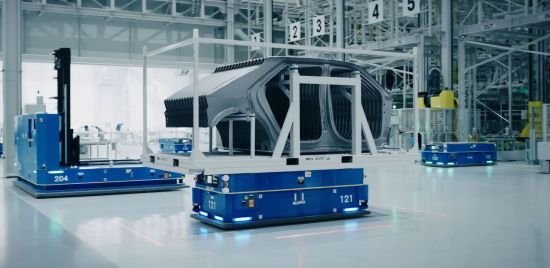
HMGMA에는 주요 계열사의 기술 역량도 어우러졌다.
현대모비스는 부지 내 글로벌 생산거점 중 최대 규모인 배터리시스템과 모듈 공장을 운영한다.
또 인근에 전기차 핵심 부품인 PE 시스템을 생산하는 별도 거점을 마련했다.
현대글로비스는 HMGMA 물류센터를 통해 부품 공급을 전반적으로 관리한다.
물류센터에는 비전 카메라를 장착한 자율비행 드론이 부품 현황을 실시간으로 파악하고, AGV가 완성차 한 대분의 부품을 실어 차량 제조 컨베이어에 연결한다.
현대제철은 초고강도강을 포함한 자동차용 강판을 가공해 프레스 공장에 공급하고, 현대트랜시스는 연간 42만대 규모의 생산능력을 바탕으로 시트를 생산한다.
현대위아는 로봇 기술 역량을 바탕으로 물류 자동화를 지원한다.
현대로템은 차량 강판을 차체 패널로 만들어주는 서보 프레스 설비를 공급한다.
노경조 기자 felizkj@asiae.co.kr
<ⓒ투자가를 위한 경제콘텐츠 플랫폼, 아시아경제 무단전재 배포금지>